Forged for Impact – The Ultra-Tough Steel Alloy Born at IDEELab
- IDEELab | Mississippi State University
- Apr 11
- 2 min read
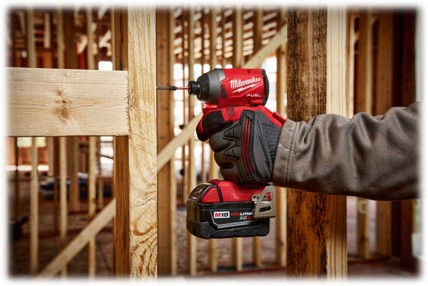
A cracked drill bit might seem like a minor inconvenience—unless you’re drilling through concrete on a job site with a tight deadline. In industries where every second counts and every tool must perform flawlessly, material failure is not an option. That’s where IDEELab stepped in.
At Mississippi State University, researchers at the Institute for Design and Engineering Evaluation (IDEE) Lab have developed a novel ultra-high-strength steel alloy, designed specifically to outperform traditional tool steels in demanding environments. What makes it revolutionary? This alloy achieves the rare balance between ductility and durability—traits that are often difficult to combine.
The Problem with Traditional Tool Steels
Conventional steel alloys used in drill bits and other impact tools often face a tradeoff:
Hard steels resist wear but are prone to brittleness and cracking under shock loads.
Ductile steels bend instead of break but wear out faster, reducing tool lifespan.
Striking the perfect balance between impact toughness, wear resistance, and manufacturability has long been a challenge in the materials science world—until now.
The IDEELab Solution
Led by faculty and graduate student metallurgists, IDEELab engineers conducted a series of high-strain rate experiments and microstructural analyses. By adjusting the alloy's chemical composition and heat treatment profiles, they unlocked a microstructure that resists cracking under shock and offers prolonged performance under abrasive conditions.
Key features of the new alloy:
Enhanced impact fatigue resistance
Superior microstructural grain refinement
Optimized hardness for long-term edge retention
This innovation was tested in both simulated environments and real-world field trials, making it industry-ready before leaving the lab.
From the Lab to Milwaukee Tool
This wasn't just a research paper—it was a product waiting to happen.
Milwaukee Tool, an industry leader in professional-grade power tools, saw the potential and moved quickly to license the alloy. Their engineering teams collaborated with IDEELab researchers to integrate the material into their premium line of impact-rated accessories, including drill bits and driver tips.
Thanks to this partnership:
Contractors using Milwaukee tools now benefit from longer-lasting accessories that hold up under extreme torque.
The IDEELab team gained an incredible success story that proves their research isn’t just theoretical—it’s practical, profitable, and game-changing.
The Bigger Picture
This breakthrough demonstrates how IDEELab’s focus on materials testing, mechanical design, and industry collaboration fuels real progress. It’s also a prime example of how university research can lead directly to economic development, technology transfer, and workforce innovation.
Conclusion
From atomic-scale alloys to real-world performance, this new steel formulation is a material solution forged with purpose. And it’s already transforming how professionals work on job sites across the country. That’s the IDEELab way—engineer better, build stronger, and never settle.
コメント